Refrigeration Dryer
Exceptional Energy Efficiency
Gamma Gas refrigeration dryer incorporates cutting-edge energy-efficient technologies that significantly reduce energy consumption. The optimized design ensures maximum drying efficiency with minimal energy usage, helping customers reduce operational costs.
Advanced Cooling System
Equipped with a state-of-the-art cooling system, our machines quickly achieve the required low temperatures, enhancing both the speed and quality of the drying process. This system ensures consistent and uniform drying results.
User-Friendly Operation
We prioritize user experience by designing an interface that is easy to operate. Even non-specialists can easily master the equipment, substantially reducing the risk of operational errors.
Long-Term Stability
Constructed with high-quality materials, our machines are built to last. Strict quality control processes ensure that each unit operates reliably over the long term, minimizing maintenance needs and costs.
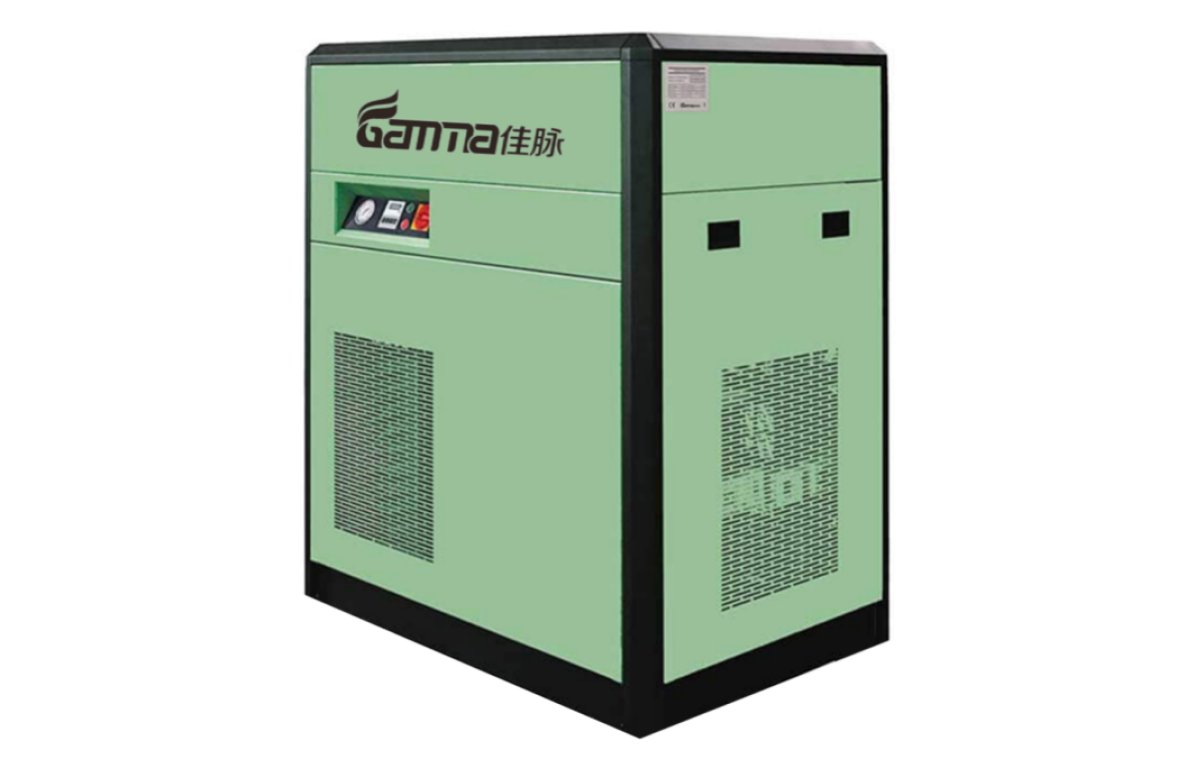
Adsorption Dryer
High-Efficiency Adsorbents: Gamma Gas adsorption dryer is filled with premium desiccants to get exceptional moisture absorption capabilities and longevity, maintaining consistent low-dew-point drying performance across various operating conditions.
Energy Efficiency: Integrated with advanced computer control panels, precisely govern the dryer's operational cycles, including automatic tower switching for continuous operation with minimized energy consumption. Microprocessor-controlled technology adapts working parameters dynamically based on real-time demand, ensuring an energy-efficient run.
High Stability: Designed to minimize pressure loss during gas flow, utilize low-resistance pneumatic valves and optimized piping layouts to preserve the overall efficiency of compressed air systems. Robust control systems and high-quality components ensure prolonged, uninterrupted operation with enhanced reliability and stability, reducing downtime risks.
Ease of Maintenance: Modular and disassemble-friendly designs facilitate easy maintenance and desiccant replacement, minimizing maintenance costs and downtime. Utilizing eco-friendly materials and designs, along with recyclable or regenerable desiccants, aligns with sustainability goals.
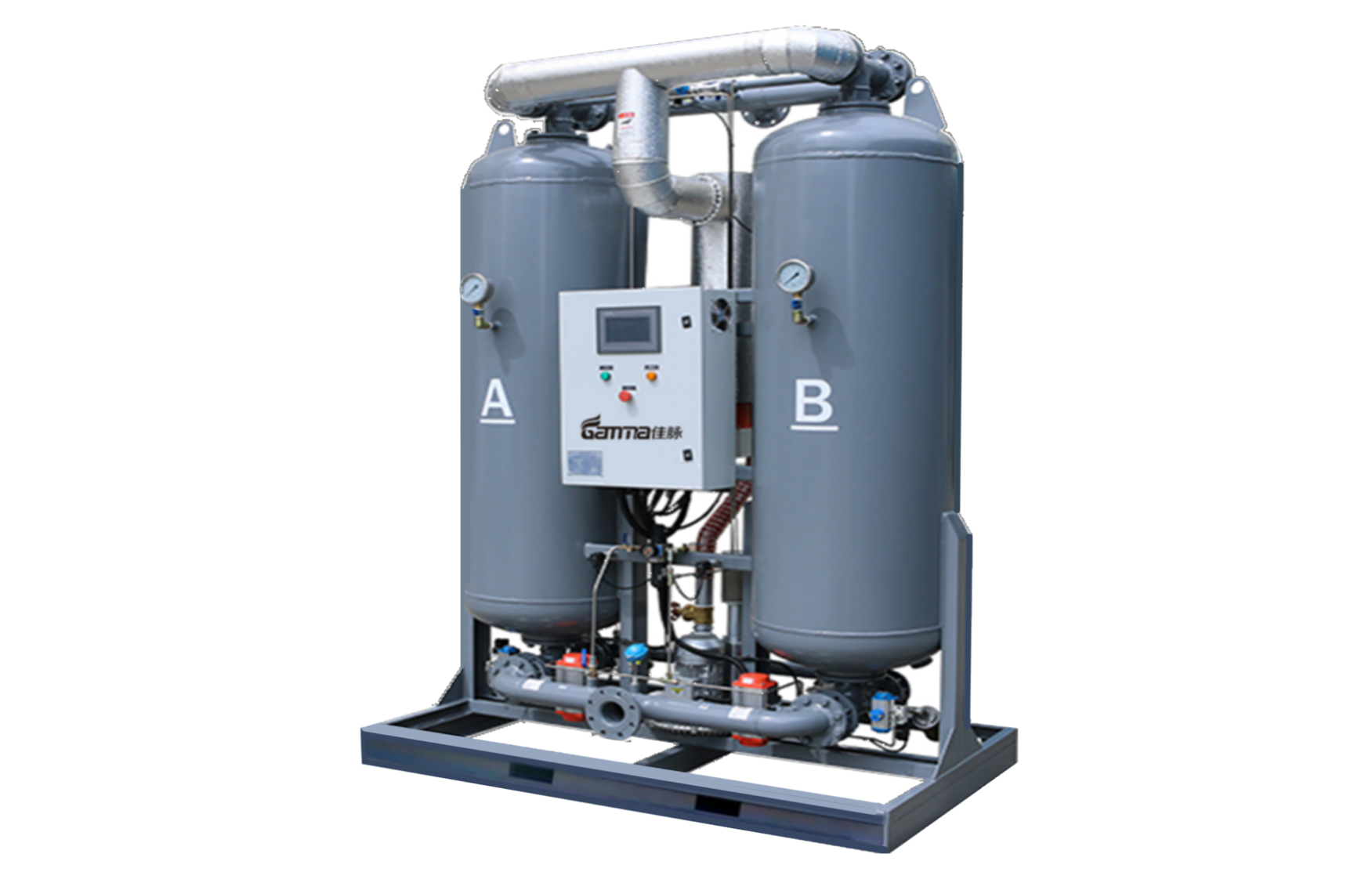
Gas compressors
Oil-free design: Gamma Gas nitrogen compressors and oxygen compressors are oil-free design, which means no lubricating oil is used in the compression process. This eliminates the risk of oil contamination, making it particularly important for applications that require high purity nitrogen and oxygen.
Environmental friendly: As oil-free compressor does not require oil lubrication, it reduces the generation and disposal issues of hazardous waste oil, thereby lowering the overall environmental impact.
Use of special materials: The friction sealing elements such as piston rings and guide rings are made of self-lubricating special materials. These materials not only reduce the dependence on lubricants but may also enhance the durability and service life of the components.
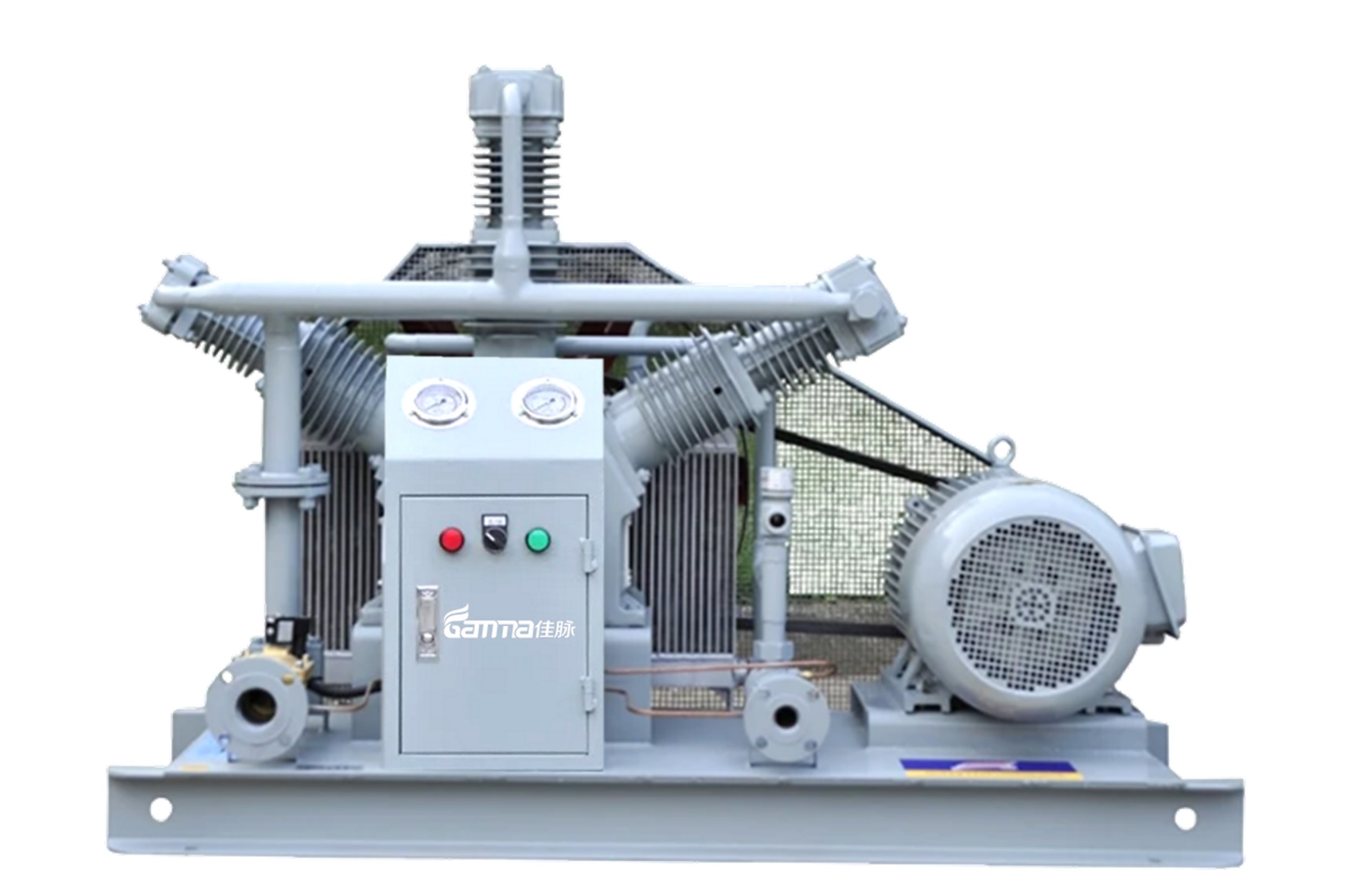
Carbon purifier
Principle: Raw material gas (common nitrogen, N2) containing oxygen (O2) reacts with excess carbon (C) under high temperature conditions to produce CO2. After the CO2 is removed, product gas (high-purity nitrogen) is obtained. The chemical reaction is: C + O2 → CO2.
Carbon-based purification is applicable in scenarios where both hydrogen (H2) and oxygen (O2) content in nitrogen gas have strict requirements. For the two-step method of producing high-purity nitrogen using Pressure Swing Adsorption followed by purification (PSA+Purification), the purity of raw material gas, common nitrogen, at the PSA outlet is typically 99.9%.
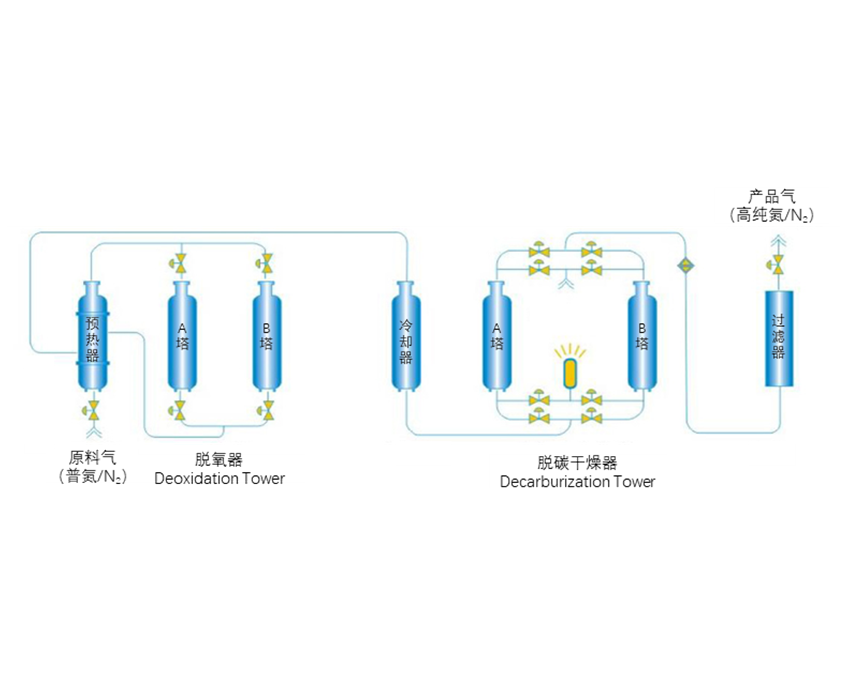
Hydrogen purifier
Process: The feed gas (common nitrogen) is mixed with a small amount of hydrogen (H2) and then enters a reactor containing palladium catalyst. In the reactor, the oxygen (O2) present in the feed gas reacts with hydrogen (H2) to form water vapor (H2O). After passing through a water separator and an adsorption dryer to remove moisture, product gas (high-purity nitrogen) is obtained. The chemical reaction is: 2H2 + O2 → 2H2O + heat.
Hydrogenation purification is suitable for applications requiring high-purity nitrogen gas (N2) where the presence of hydrogen (H2) is not critical (typically around 500 ppm), safe and reliable source of hydrogen must be available on site.
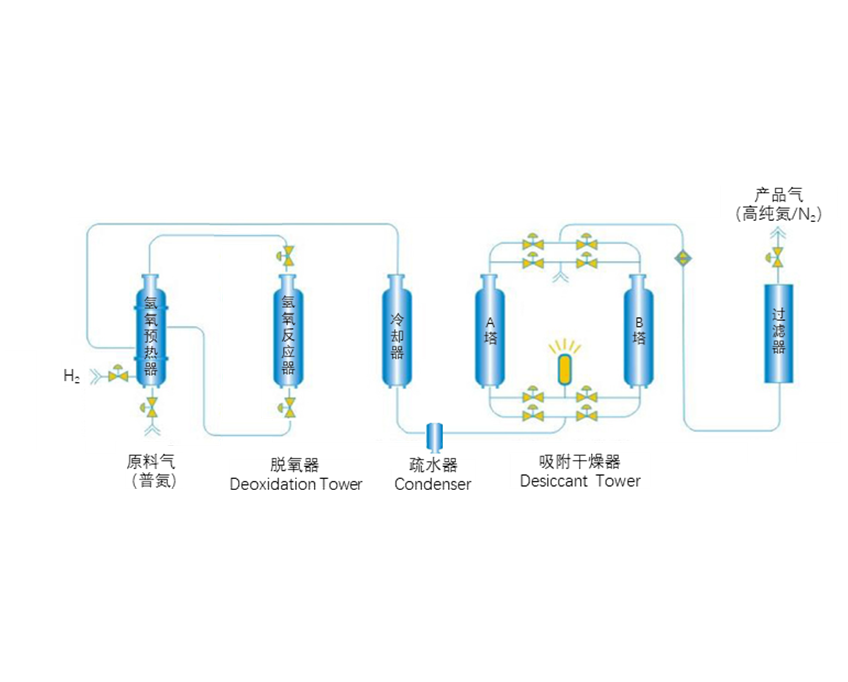